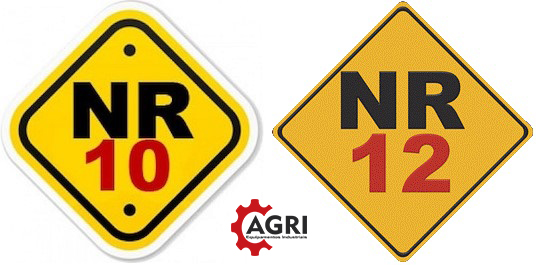
Visando reduzir os riscos de acidentes em ambientes industriais, o Ministério do Trabalho estabeleceu uma série de normas regulamentadoras de segurança e requisitos obrigatórios para garantir a proteção à saúde e à integridade física dos trabalhadores.
Entre estas normas estão a NR-10 e a NR-12. A primeira atua nas diretrizes para instalações elétricas em suas etapas de projeto, engenharia, montagem, operação e manutenção; enquanto a segunda define os procedimentos indispensáveis aos ambientes que comportam máquinas, equipamentos, operações e dispositivos de partida e parada.
O papel da NR-10 na automação industrial
O principal propósito da NR-10 é resguardar a segurança dos profissionais que trabalham direta ou indiretamente com instalações elétricas. Para tanto, a norma determina diretrizes de controle e prevenção que englobam todo o processo de transformação da energia elétrica, a incluir geração, distribuição, consumo e manutenção. Abrange-se ainda a seguridade dos serviços de eletricidade e/ou que demandam essa fonte de energia.
A norma sanciona, por exemplo, que as instalações elétricas em ambientes laborais deverão ser compatíveis com as atividades exercidas, características da indústria e equipamentos de operação. As medidas de segurança e os componentes da instalação devem ser definidos conforme fatores externos, tais como: proximidade à água ou umidade; existência de corpos sólidos; frequência de circulação de pessoas no local; grau de condutibilidade dos materiais processados ou armazenados; entre outros aspectos que possam influenciar significativamente o risco de acidentes elétricos.
A norma dispõe ainda de diretrizes de trabalho qualificado, estabelecendo que apenas profissionais habilitados por meio de cursos e treinamentos poderão exercer atividades relacionadas à eletricidade. A indústria também deverá cumprir regras que incluem o fornecimento de materiais de segurança e uniformes especiais para o trabalho.
É pertinente ressaltar que, para garantir um projeto de eletricidade industrial completamente fiel aos princípios da NR-10, é essencial contar com máquinas “inteligentes”, que conseguem antecipar riscos e prevenir acidentes de forma autônoma. Ao trabalhar com maquinários e sistemas automatizados, é possível proteger profissionais de situações perigosas como choques ou incêndios, além de prevenir danos elétricos em equipamentos.
A NR-12 no contexto da automação industrial
O objetivo máximo da NR-12 é assegurar critérios de proteção de máquinas, equipamentos e áreas operacionais com tráfego de pessoas. Também é de sua competência regular as questões técnicas relacionadas a dispositivos dinâmicos de acionamento e desligamento. Prioritariamente, a norma exige a adoção de medidas de proteção coletiva, organização do trabalho e proteção individual.
Todos os princípios da NR-12 contemplam medidas para garantir ambientes industriais salubres, capazes de prevenir acidentes e doenças laborais. Na prática, trata-se de proteger os operadores de riscos que possam ter consequências graves como esmagamento, amputações, queimaduras ou intoxicação.
Outro ponto relevante da NR-12 é que ela estimula a adesão de tecnologias mais avançadas de monitoramento, que funcionam a partir de sistemas automatizados de sensores e redes de comunicação industrial. O resultado são autênticas “fábricas inteligentes”, que aumentam não só a segurança das equipes humanas, mas também sua produtividade.
Adequando máquinas à NR-10 e NR-12
Indústrias que ainda possuem maquinários irregulares podem adequar todo o seu parque operacional às normas regulamentadoras. Para tanto, basta contar com o suporte de uma empresa de automação industrial, que ficará responsável pela “arquitetura” e implementação dos novos projetos de máquinas e sistemas.
A primeira etapa dessa adequação constitui-se de um estudo completo dos perigos da máquina. As insalubridades encontradas serão “catalogadas”, de modo a criar uma lista de alterações prioritárias.
Após conhecer e compreender todos os riscos, é desenhado o projeto elétrico, mecânico, hidráulico, pneumático e de monitoramento, arquitetando assim todos os aspectos de segurança necessários. Posteriormente, inicia-se a fabricação e implementação dos novos dispositivos, painéis, circuitos e demais itens de adequação e proteção.
Depois de passar pela “reengenharia”, a máquina deverá ser novamente documentada conforme os critérios das normas regulamentadoras que exigem, basicamente, manuais, escopos e desenhos com conteúdo sucinto e em português do Brasil. Por fim, as novas soluções da máquina e seus documentos passarão por validação, que garantirá sua implementação definitiva.
É importante destacar que, após validada, a máquina deverá ter uma “rotina” de manutenções agendadas, visando garantir sua proteção e segurança conforme as normas regulamentadoras.
Alguns dados e estatísticas importantes sobre acidentes de trabalho:
O Brasil é 4º lugar no mundo em acidentes de trabalho, com uma média de 700 mil registros de acidentes de trabalho por ano. O país fica atrás somente de China, Índia e Indonésia. A região sudeste é a responsável por 53,9% dos registros.
De acordo com o Ministério da Fazenda, entre 2012 e 2016, foram registrados 3,5 milhões de casos de acidente de trabalho em 26 estados e no Distrito Federal. Esses casos resultaram na morte de 13.363 pessoas
A Pesquisa Nacional de Saúde (PNS), realizada pelo IBGE mostrou que para cada acidente de trabalho registrado pela Previdência Social, há quase sete acidentes não declarados oficialmente.